Beleggingsmetodene for fotoresist er generelt delt inn i spinnbelegg, dyppebelegg og rullbelegg, blant hvilke spinnbelegg er det mest brukte. Ved spinnbelegg dryppes fotoresist på substratet, og substratet kan roteres med høy hastighet for å oppnå en fotoresistfilm. Etter det kan en solid film oppnås ved å varme den på en kokeplate. Spin-belegg er egnet for belegg fra ultratynne filmer (ca. 20nm) til tykke filmer på ca. 100um. Dens egenskaper er god ensartethet, jevn filmtykkelse mellom wafere, få defekter, etc., og en film med høy beleggsytelse kan oppnås.
Spin belegningsprosess
Under spinnbelegg bestemmer hovedrotasjonshastigheten til substratet filmtykkelsen til fotoresisten. Forholdet mellom rotasjonshastigheten og filmtykkelsen er som følger:
Spin=kTn
I formelen er Spin rotasjonshastigheten; T er filmtykkelsen; k og n er konstanter.
Faktorer som påvirker spinnbelegningsprosessen
Selv om filmtykkelsen bestemmes av hovedrotasjonshastigheten, er den også relatert til romtemperatur, fuktighet, fotoresistviskositet og fotoresisttype. Sammenligning av forskjellige typer fotoresistbeleggskurver er vist i figur 1.
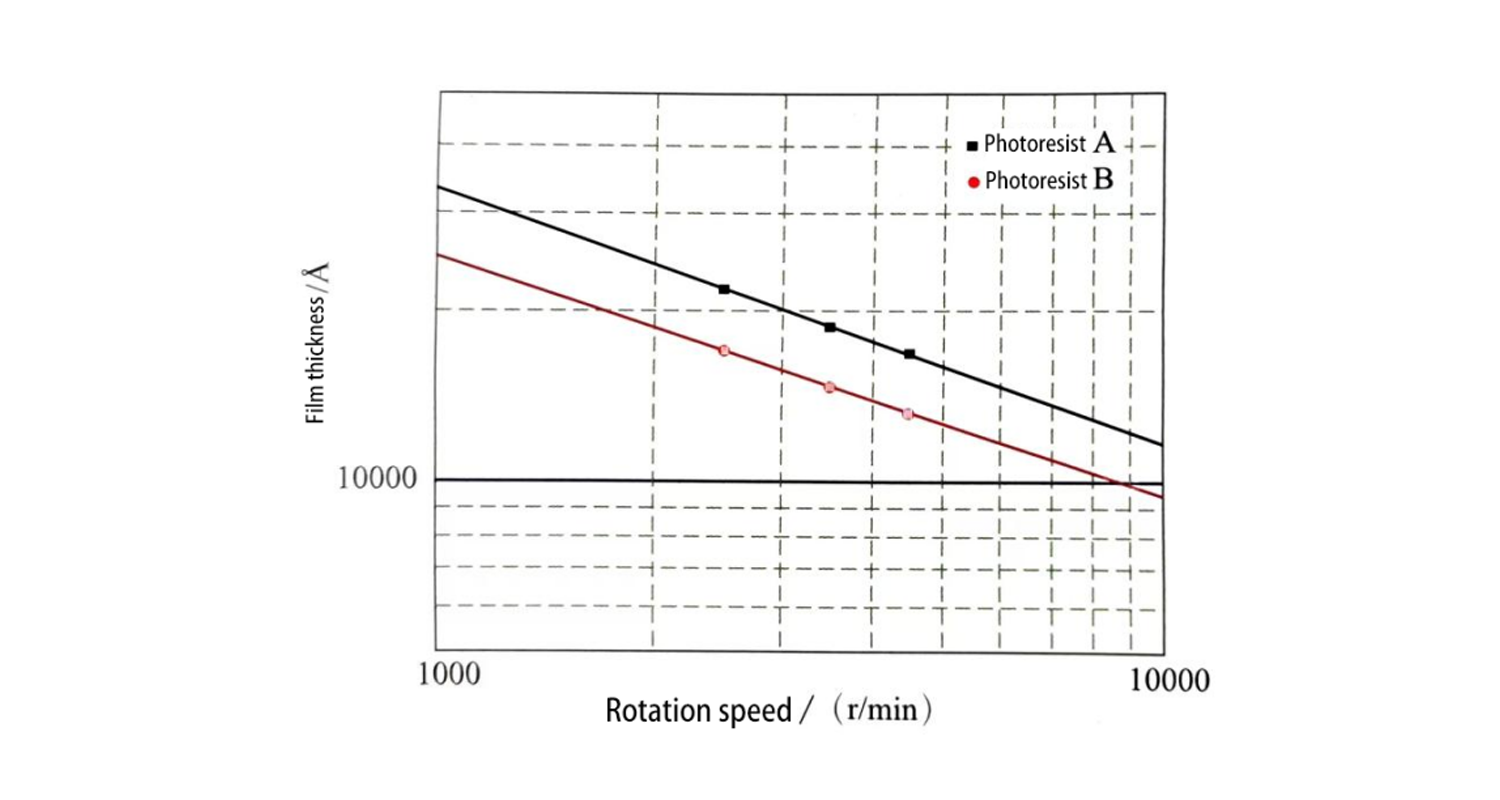
Figur 1: Sammenligning av ulike typer fotoresistbeleggskurver
Påvirkning av hovedrotasjonstid
Jo kortere hovedrotasjonstiden er, jo tykkere filmtykkelse. Når hovedrotasjonstiden økes, jo tynnere blir filmen. Når den overstiger 20s, forblir filmtykkelsen nesten uendret. Derfor er hovedrotasjonstiden vanligvis valgt til å være mer enn 20 sekunder. Forholdet mellom hovedrotasjonstiden og filmtykkelsen er vist i figur 2.
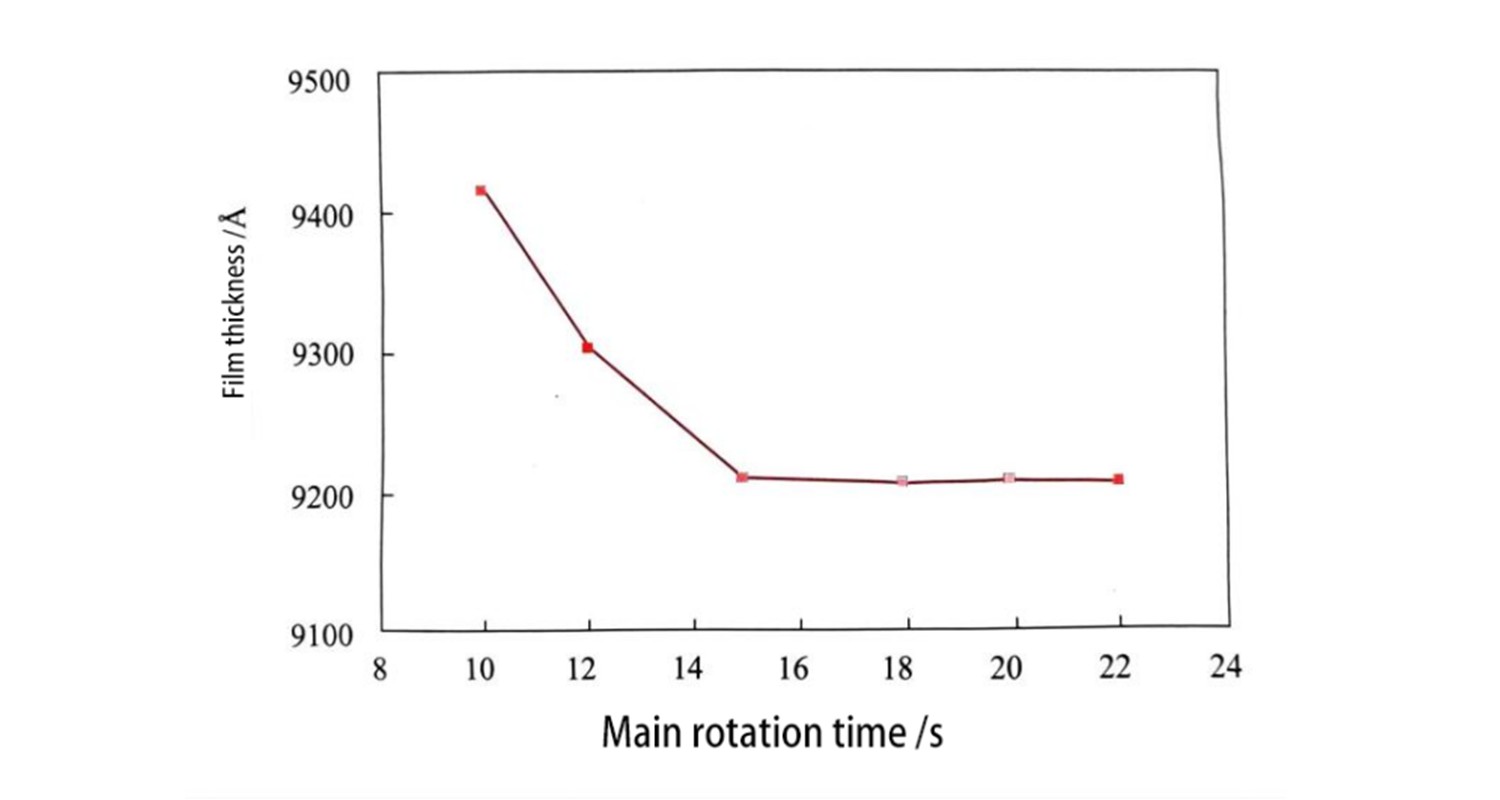
Figur 2: Sammenheng mellom hovedrotasjonstid og filmtykkelse
Når fotoresisten dryppes på substratet, selv om den påfølgende hovedrotasjonshastigheten er den samme, vil rotasjonshastigheten til substratet under dryppingen påvirke den endelige filmtykkelsen. Tykkelsen på fotoresistfilmen øker med økningen av substratets rotasjonshastighet under dryppingen, noe som skyldes påvirkningen av løsningsmiddelfordampning når fotoresisten foldes ut etter drypping. Figur 3 viser forholdet mellom filmtykkelsen og hovedrotasjonshastigheten ved forskjellige substratrotasjonshastigheter under fotoresistdryppingen. Det kan sees av figuren at med økningen av rotasjonshastigheten til det dryppende substratet, endres filmtykkelsen raskere, og forskjellen er mer tydelig i området med lavere hovedrotasjonshastighet.
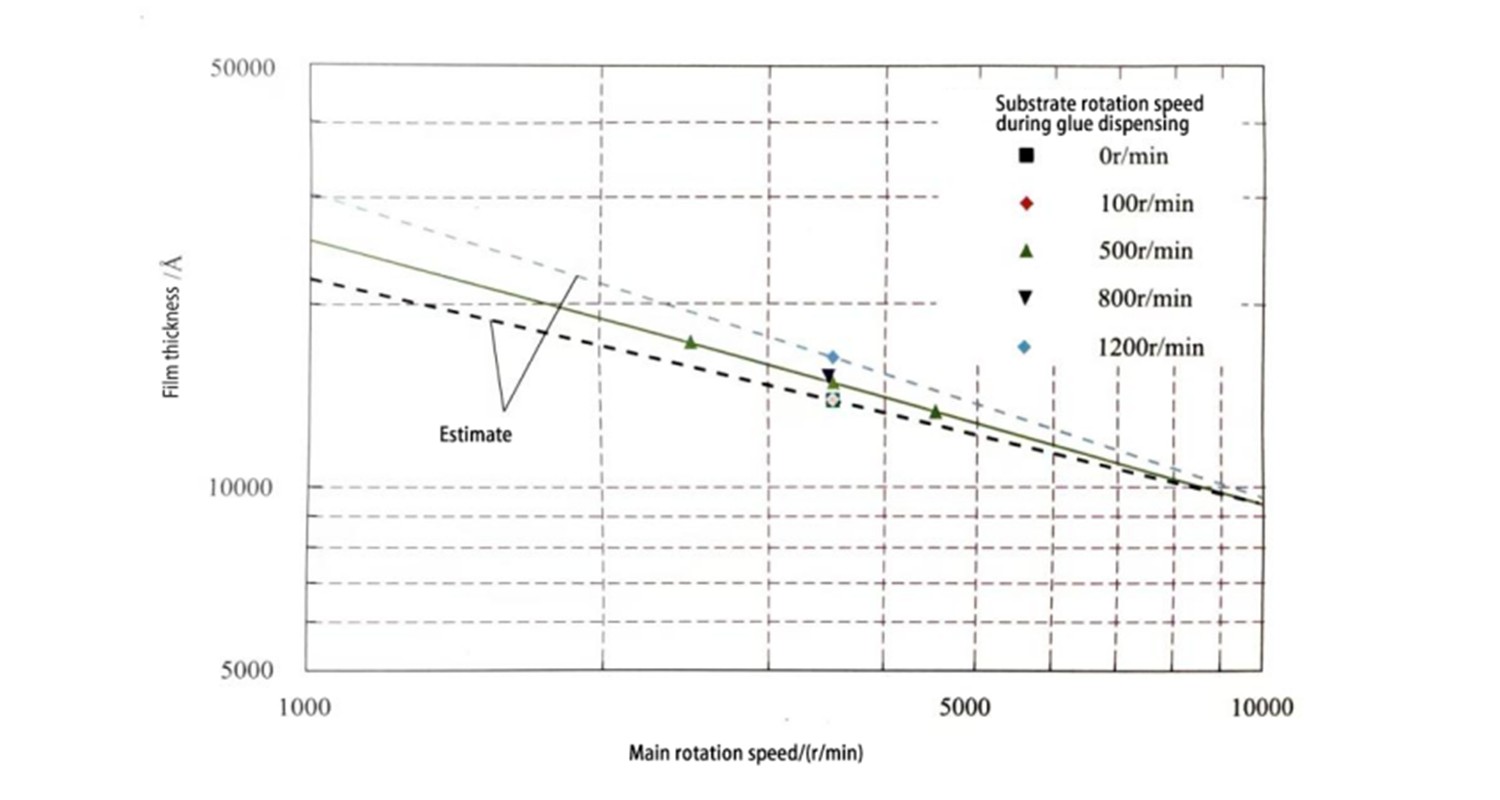
Figur 3: Forholdet mellom filmtykkelse og hovedrotasjonshastighet ved forskjellige substratrotasjonshastigheter under fotoresistdispensering
Effekt av fuktighet under belegg
Når fuktigheten synker, øker filmtykkelsen, fordi reduksjonen i fuktighet fremmer fordampningen av løsningsmidlet. Imidlertid endres ikke filmtykkelsesfordelingen vesentlig. Figur 4 viser forholdet mellom fuktighet og filmtykkelsesfordeling under belegg.
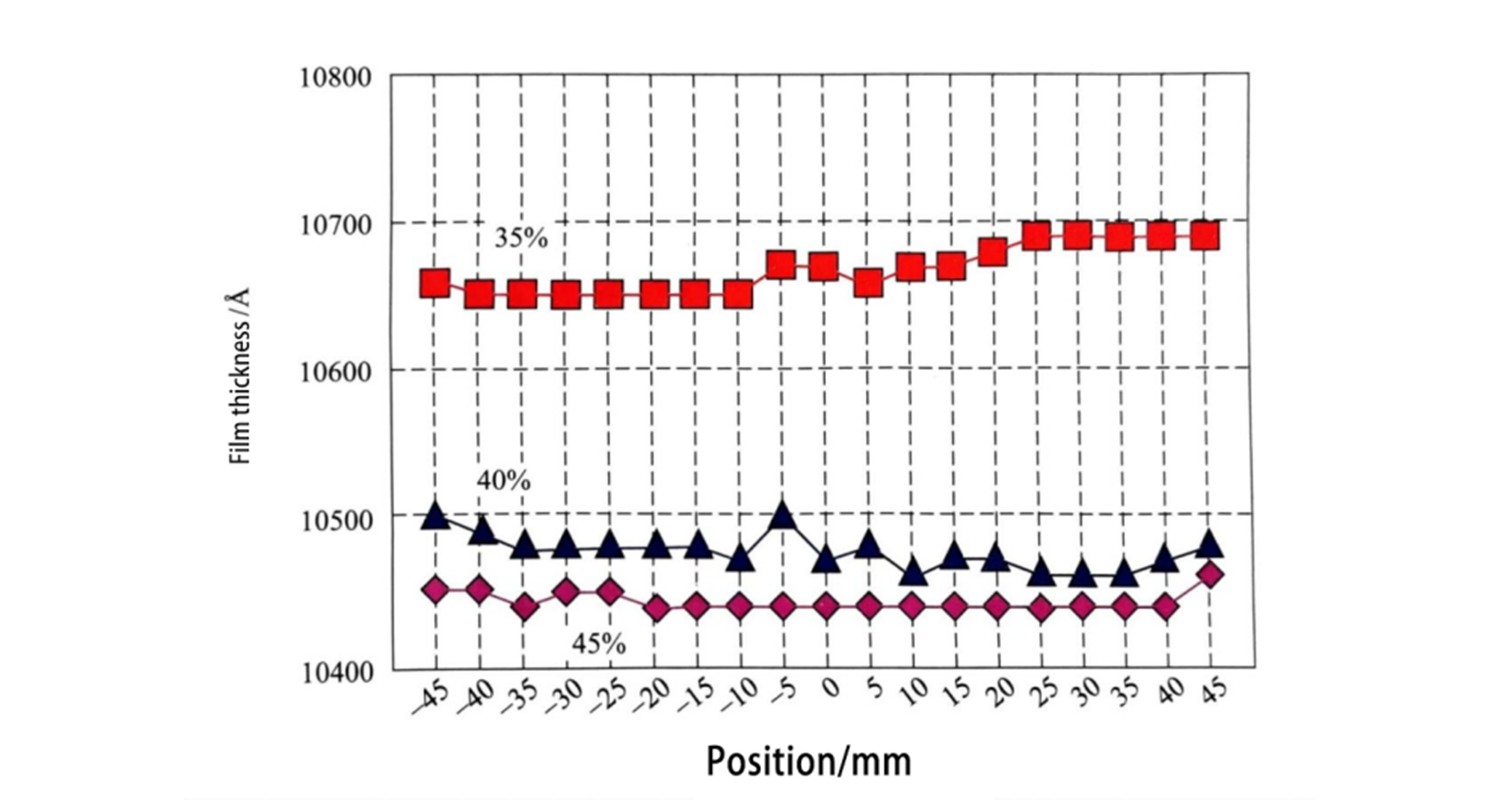
Figur 4: Sammenheng mellom fuktighet og filmtykkelsesfordeling under belegg
Effekt av temperatur under belegg
Når innetemperaturen stiger, øker filmtykkelsen. Det kan sees fra figur 5 at fordelingen av fotoresistfilmtykkelsen endres fra konveks til konkav. Kurven i figuren viser også at høyest jevnhet oppnås når innetemperaturen er 26°C og fotoresisttemperaturen er 21°C.
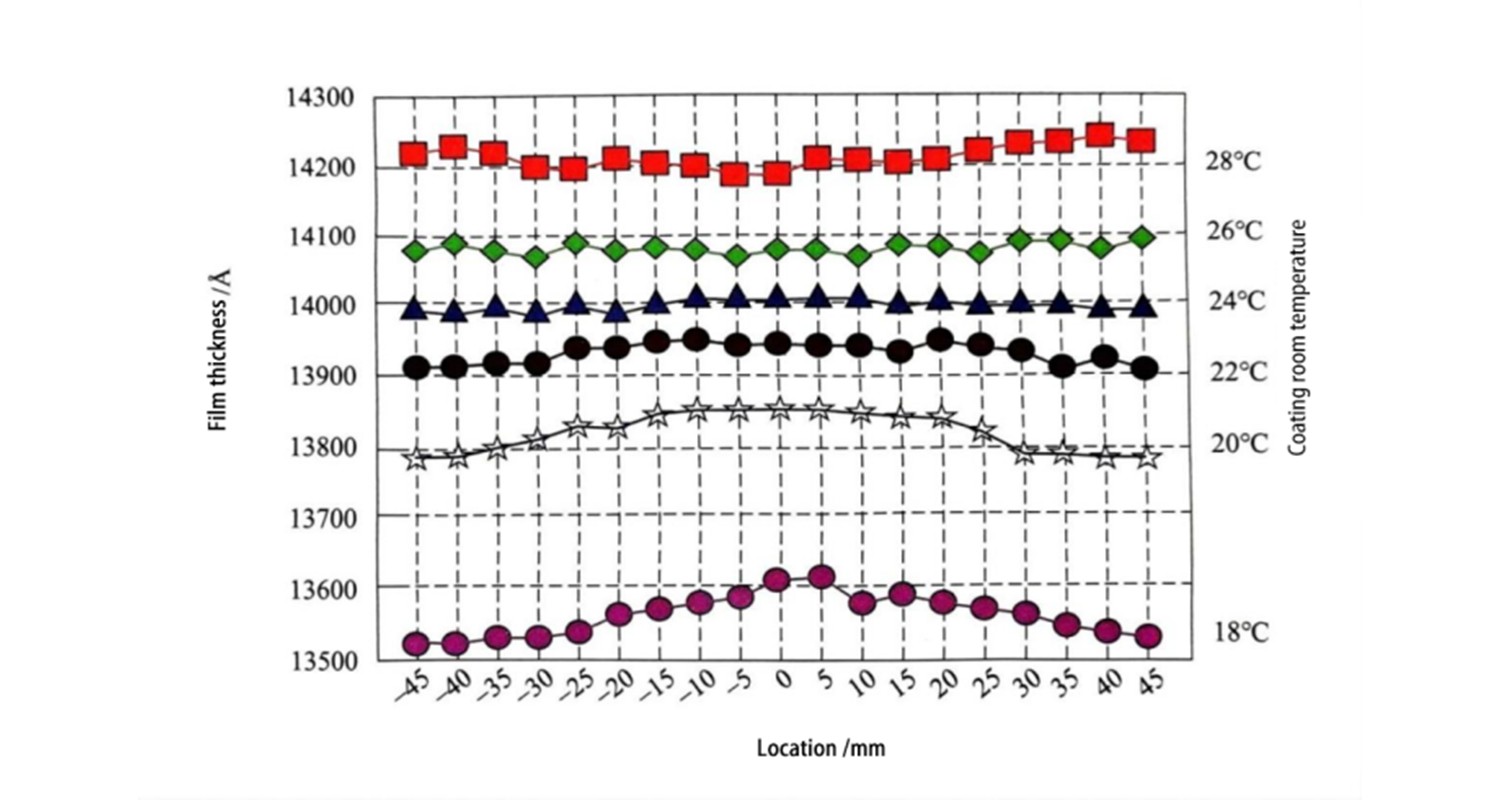
Figur 5: Sammenheng mellom temperatur og filmtykkelsesfordeling under belegg
Effekt av eksoshastighet under belegg
Figur 6 viser forholdet mellom eksoshastighet og filmtykkelsesfordeling. I fravær av eksos viser det at midten av waferen har en tendens til å tykne. Økning av eksoshastigheten vil forbedre jevnheten, men økes den for mye vil jevnheten avta. Det kan sees at det er en optimal verdi for eksoshastigheten.
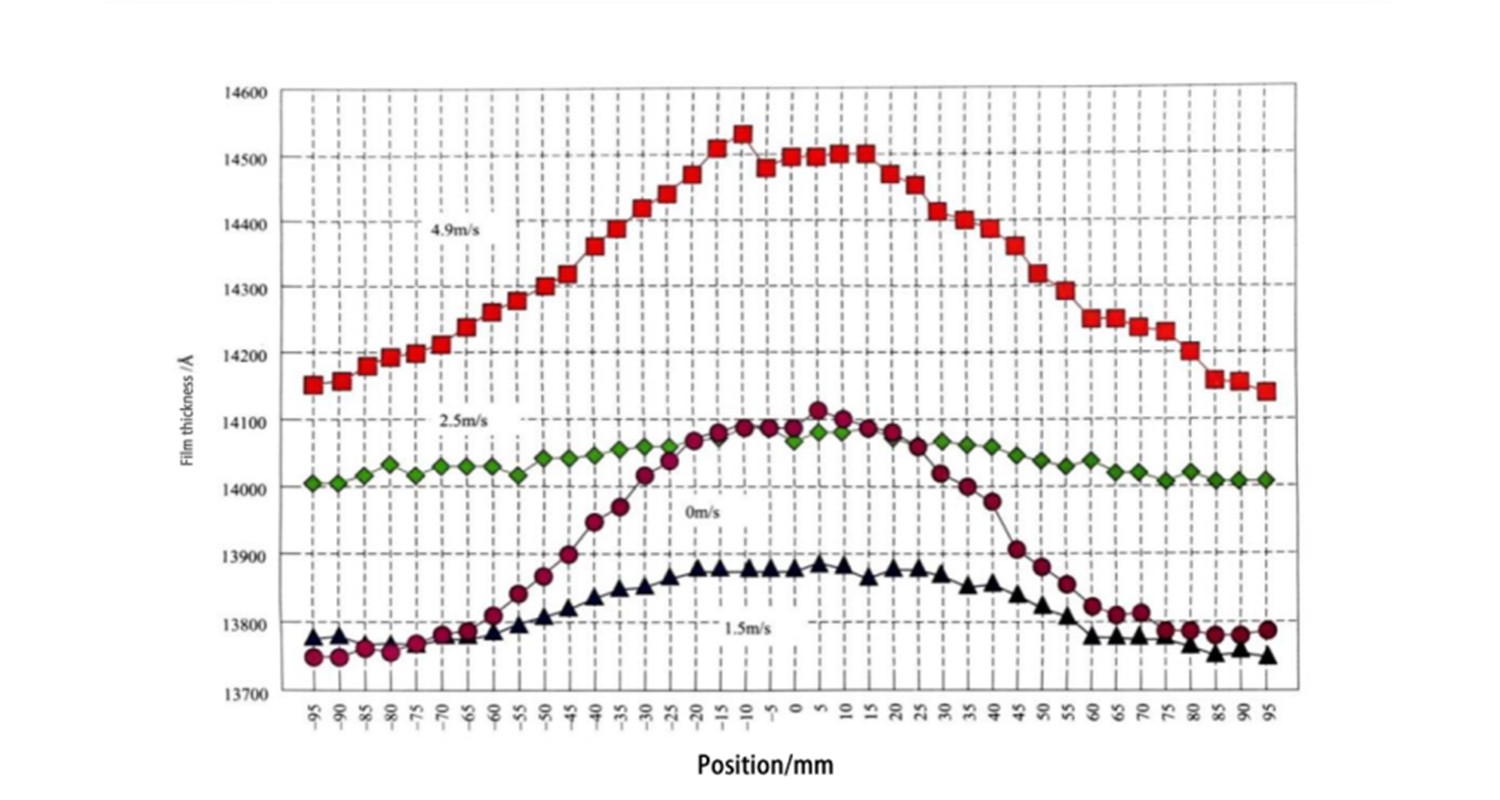
Figur 6: Sammenheng mellom eksoshastighet og filmtykkelsesfordeling
HMDS behandling
For å gjøre fotoresisten mer beleggbar, må waferen behandles med heksametyldisilazan (HMDS). Spesielt når fuktighet festes til overflaten av Si-oksidfilmen, dannes silanol, noe som reduserer vedheften til fotoresisten. For å fjerne fuktighet og dekomponere silanol, varmes waferen vanligvis opp til 100-120°C, og tåke HMDS introduseres for å forårsake en kjemisk reaksjon. Reaksjonsmekanismen er vist i figur 7. Gjennom HMDS-behandling blir den hydrofile overflaten med liten kontaktvinkel en hydrofob overflate med stor kontaktvinkel. Oppvarming av waferen kan oppnå høyere fotoresist-adhesjon.
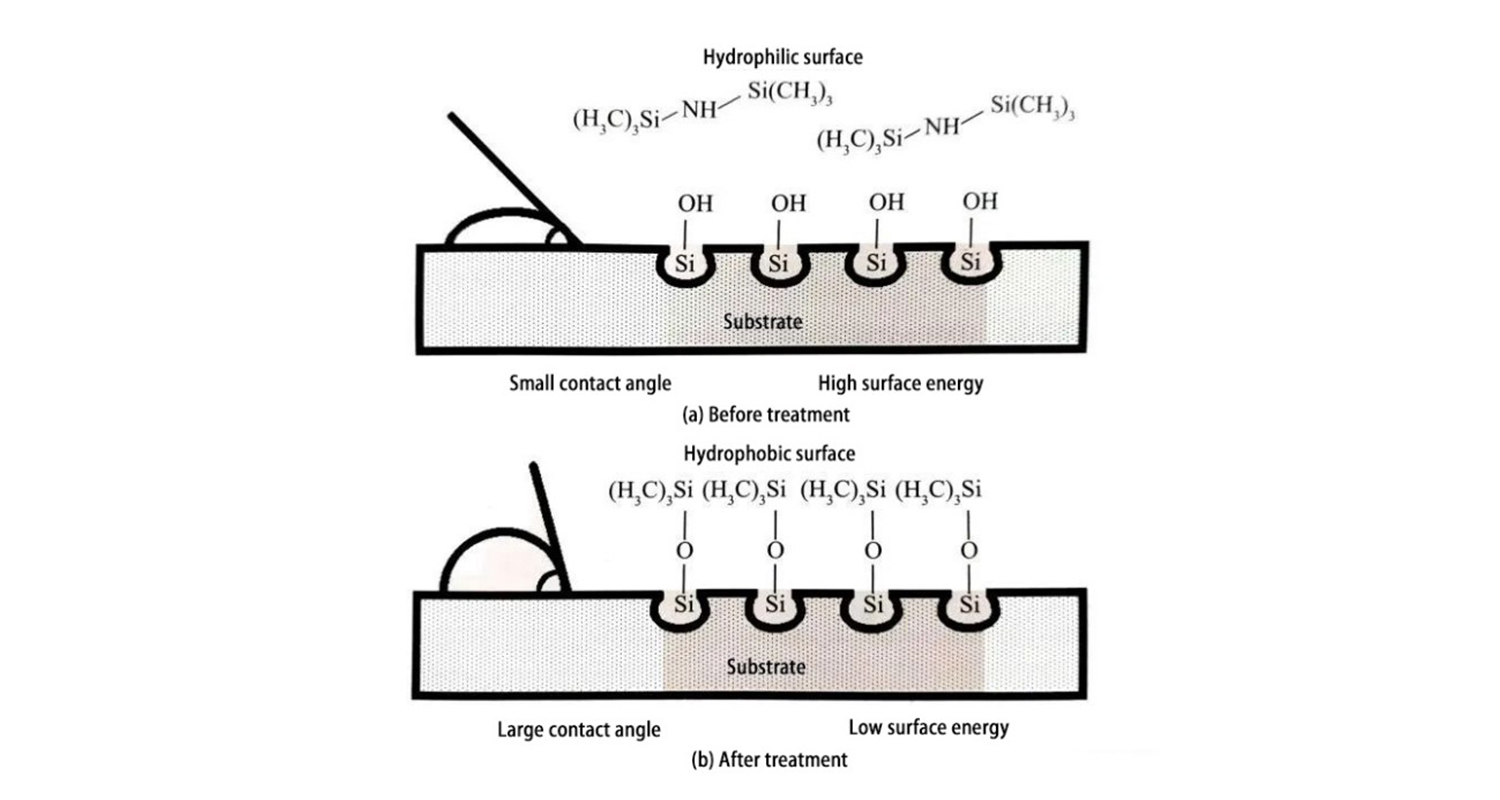
Figur 7: HMDS-reaksjonsmekanisme
Effekten av HMDS-behandling kan observeres ved å måle kontaktvinkelen. Figur 8 viser forholdet mellom HMDS-behandlingstid og kontaktvinkel (behandlingstemperatur 110°C). Substratet er Si, HMDS-behandlingstiden er større enn 1 min, kontaktvinkelen er større enn 80°, og behandlingseffekten er stabil. Figur 9 viser forholdet mellom HMDS behandlingstemperatur og kontaktvinkel (behandlingstid 60s). Når temperaturen overstiger 120 ℃, reduseres kontaktvinkelen, noe som indikerer at HMDS brytes ned på grunn av varme. Derfor utføres HMDS-behandling vanligvis ved 100-110 ℃.
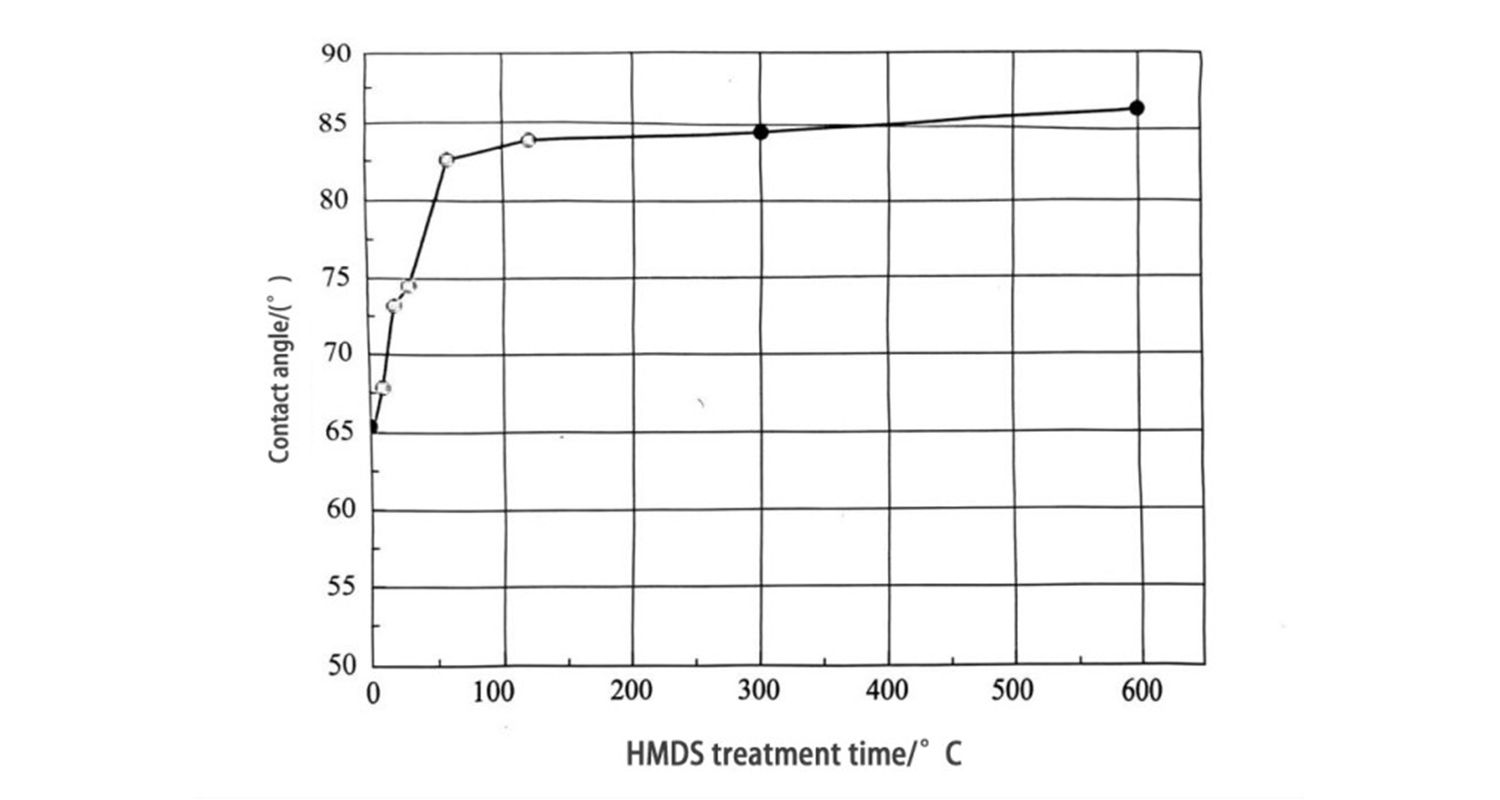
Figur 8: Sammenheng mellom HMDS-behandlingstid
og kontaktvinkel (behandlingstemperatur 110 ℃)
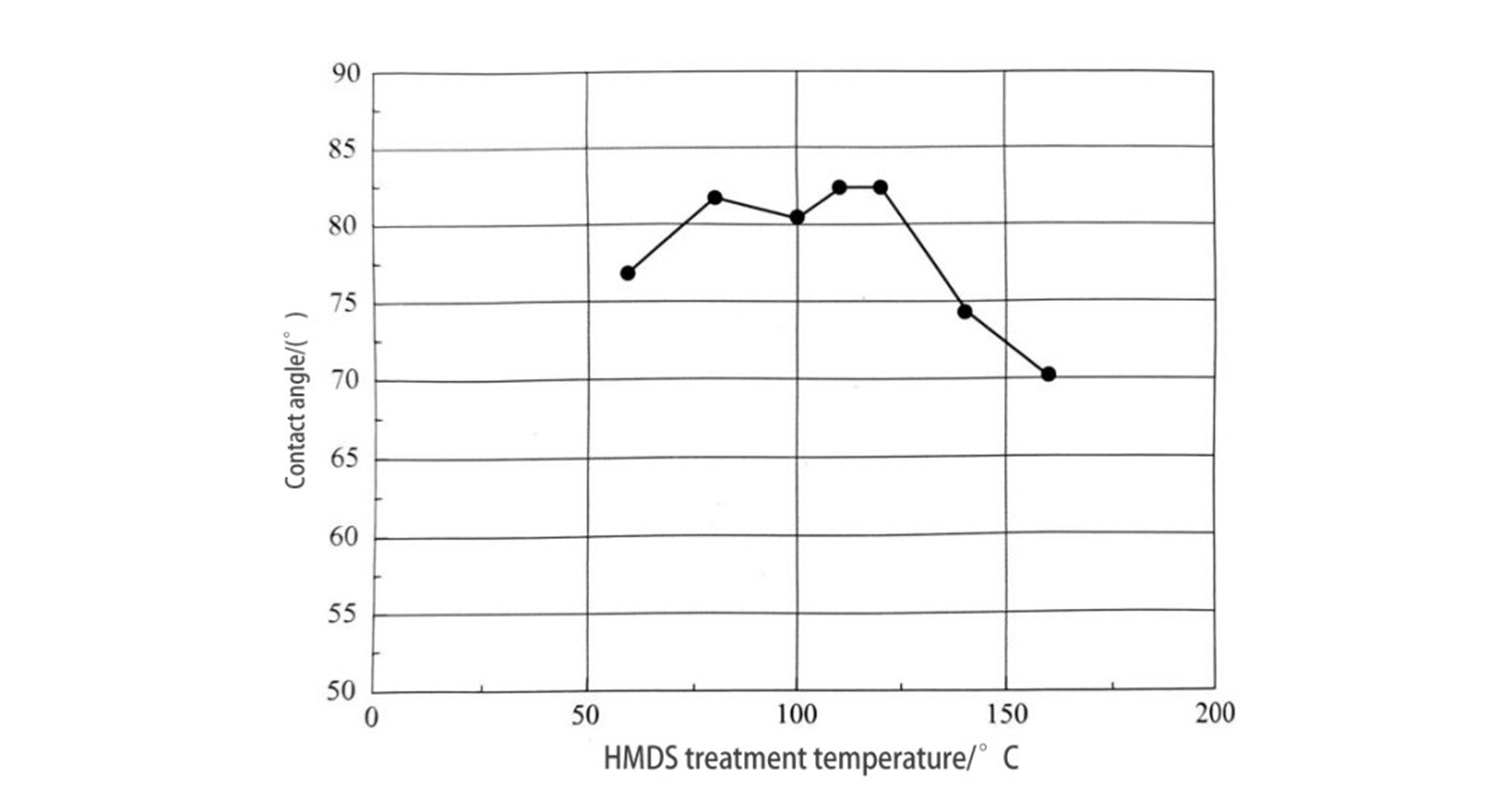
Figur 9: Sammenheng mellom HMDS behandlingstemperatur og kontaktvinkel (behandlingstid 60s)
HMDS-behandling utføres på et silisiumsubstrat med en oksidfilm for å danne et fotoresistmønster. Oksydfilmen blir deretter etset med flussyre med en buffer tilsatt, og det er funnet at etter HMDS-behandling kan fotoresistmønsteret holdes fra å falle av. Figur 10 viser effekten av HMDS-behandling (mønsterstørrelsen er 1um).
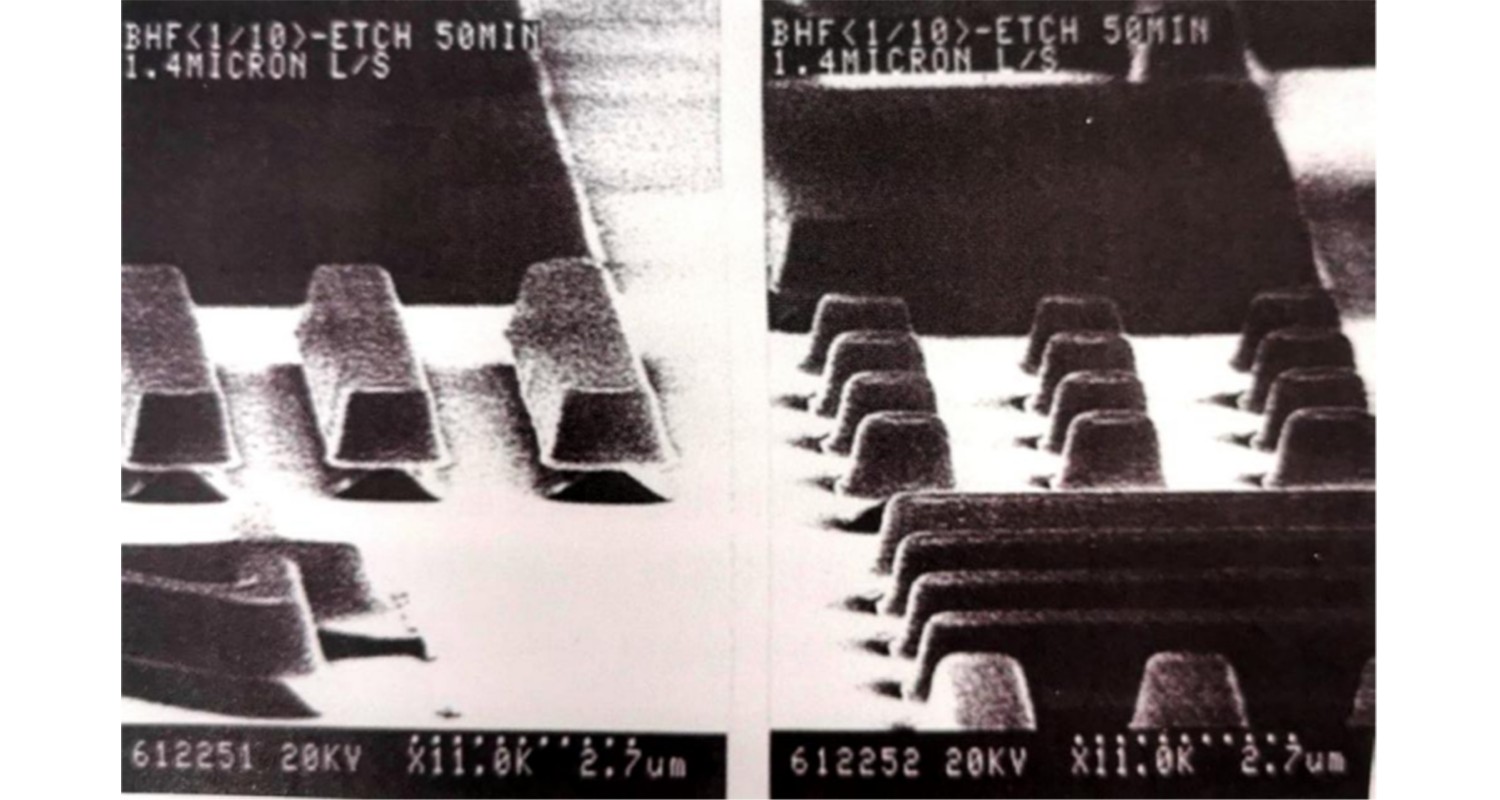
Figur 10: HMDS-behandlingseffekt (mønsterstørrelsen er 1um)
Forbaking
Ved samme rotasjonshastighet, jo høyere forbakingstemperatur, jo mindre filmtykkelse, noe som indikerer at jo høyere forbakingstemperatur, jo mer løsemiddel fordamper, noe som resulterer i en tynnere filmtykkelse. Figur 11 viser forholdet mellom forsteketemperaturen og Dills A-parameter. A-parameteren indikerer konsentrasjonen av det lysfølsomme middelet. Som det fremgår av figuren, når forstekingstemperaturen stiger til over 140°C, synker A-parameteren, noe som indikerer at det lysfølsomme middelet brytes ned ved en temperatur høyere enn dette. Figur 12 viser spektraltransmittansen ved forskjellige forstekingstemperaturer. Ved 160°C og 180°C kan en økning i transmittans observeres i bølgelengdeområdet 300-500nm. Dette bekrefter at det lysfølsomme middelet er bakt og dekomponert ved høye temperaturer. Forsteketemperaturen har en optimal verdi, som bestemmes av lysegenskaper og følsomhet.
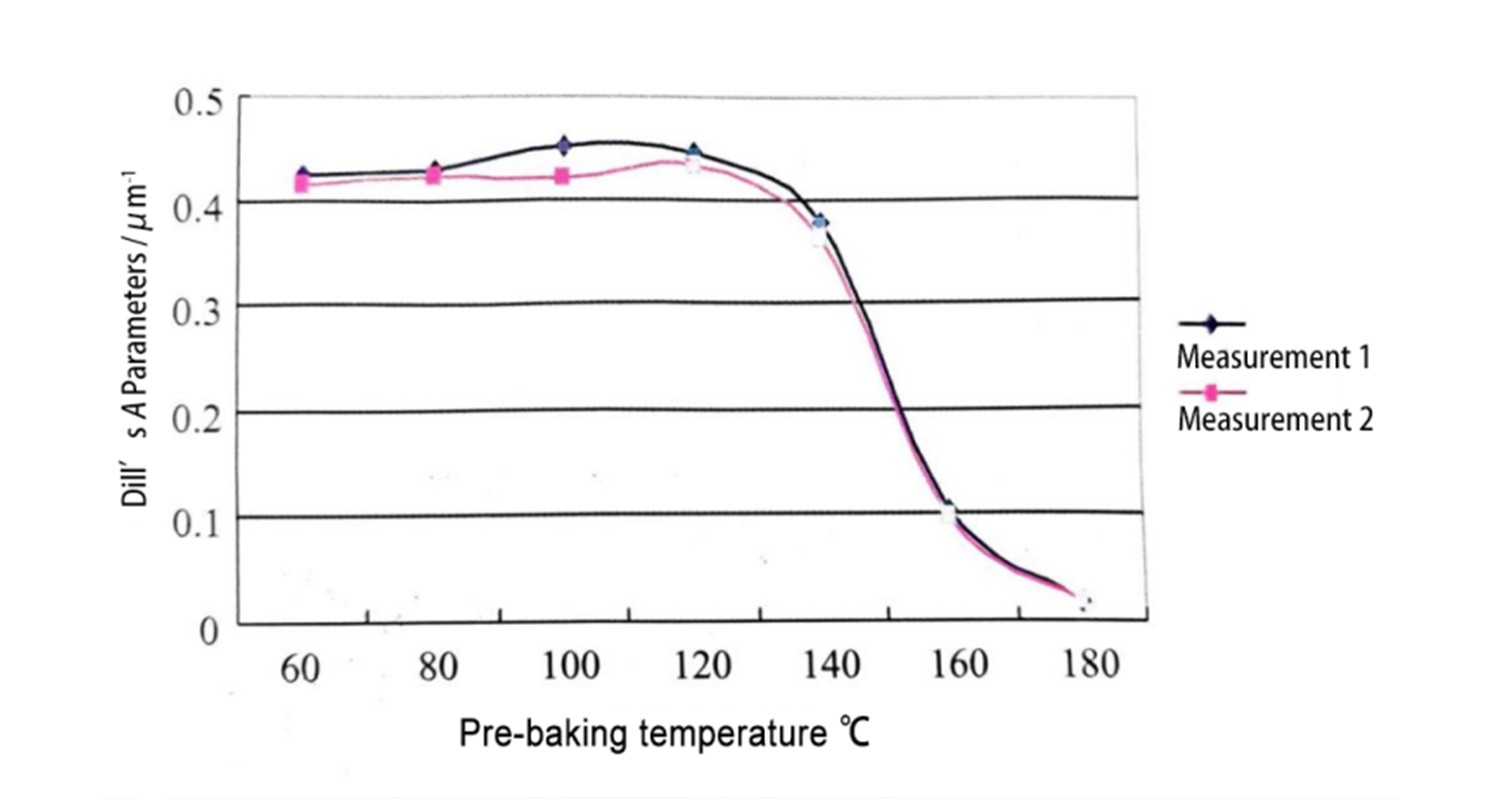
Figur 11: Sammenheng mellom forsteketemperatur og Dills A-parameter
(målt verdi av OFPR-800/2)
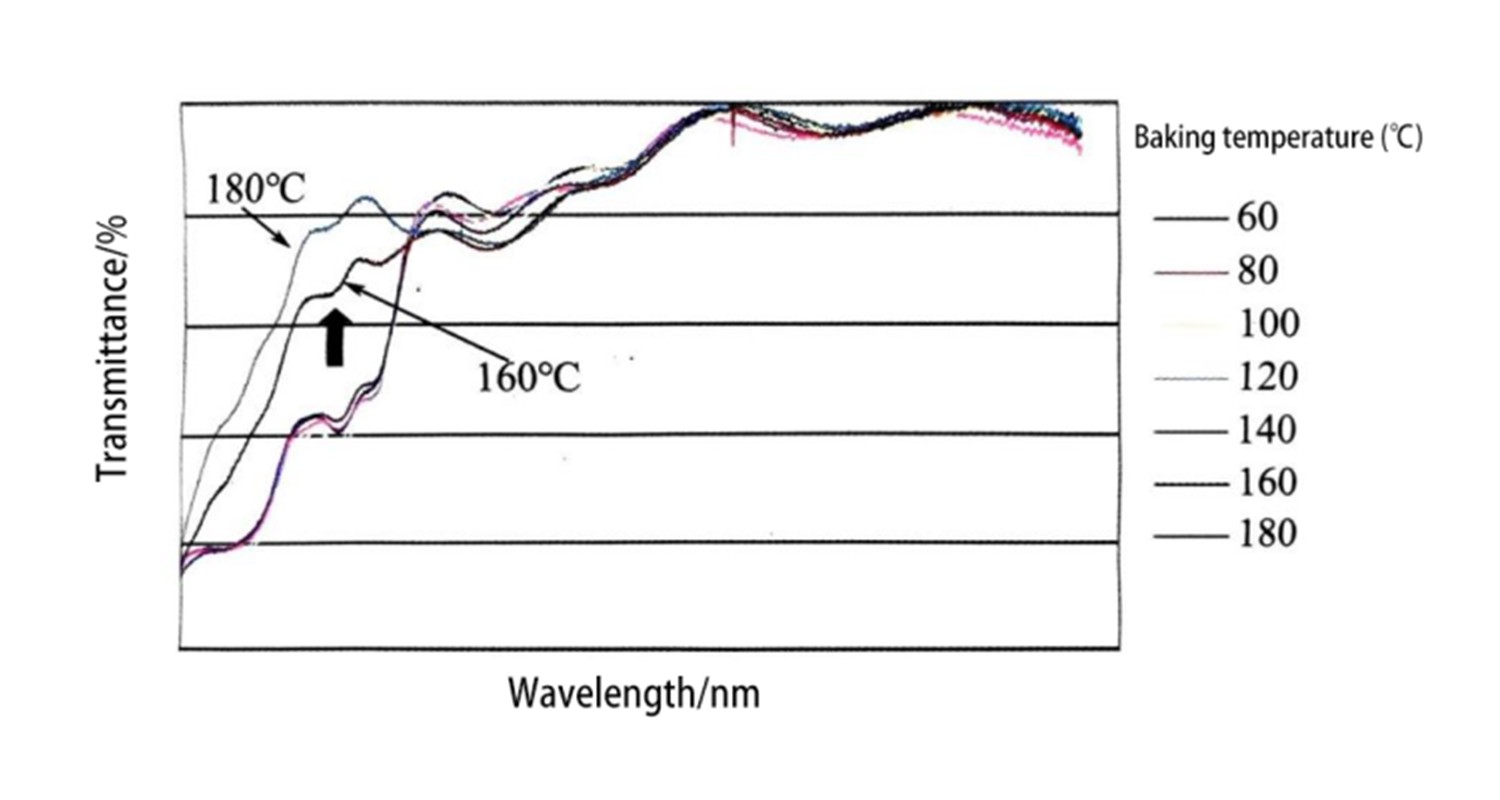
Figur 12: Spektral transmittans ved forskjellige forstekingstemperaturer
(OFPR-800, 1um filmtykkelse)
Kort sagt har spinnbeleggmetoden unike fordeler som presis kontroll av filmtykkelse, høy kostnadsytelse, milde prosessforhold og enkel operasjon, så den har betydelige effekter for å redusere forurensning, spare energi og forbedre kostnadsytelsen. De siste årene har spinnbelegg fått økende oppmerksomhet, og påføringen har gradvis spredt seg til ulike felt.
Innleggstid: 27. november 2024